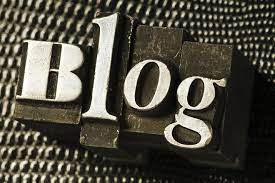
SERTLİK ÖLÇME DENEYİ NEDİR?
SERTLİK ÖLÇME DENEYİ
Malzemeler üzerinde yapılan en genel deney, sertliğinin ölçülmesidir. Bunun başlıca sebebi, deneyin basit oluşu ve diğerlerine oranla numuneyi daha az tahrip etmesidir. Diğer avantajı ise, bir malzemenin sertliği ile diğer mekanik özellikleri arasında paralel bir ilişkinin bulunmasıdır. Örneğin çeliklerde, çekme mukavemeti sertlik ile doğru orantılıdır; dolayısıyla, yapılan basit sertlik ölçmesi neticesinde malzemenin mukavemeti hakkında bir fikir edinmek mümkündür.
Sertlik izafi bir ölçü olup sürtünmeye, çizmeğe, kesmeğe ve plastik deformasyona karşı direnç olarak tarif edilir. Laboratuarlarda özel cihazlarla yapılan setlik ölçümlerindeki değer, malzemenin plastik deformasyona karşı gösterdiği dirençtir.
Sertlik ölçme genellikle, konik veya küresel Standard bir ucun malzemeye batırılmasına karşı malzemenin gösterdiği direnci ölçmekten ibarettir. Uygun olarak seçilen sert uç, tatbik edilen bir yük altında malzemeye batırıldığında malzeme üzerinde bir iz bırakacaktır. Genel deyimle malzemenin sertliği, bu izin büyüklüğü ile ters orantılıdır. [1]
Bugün laboratuarlarda uygulanan sertlik ölçme yöntemleri şunlardır:
♦ Brinell sertlik ölçme yöntemi,
♦ Rockwell sertlik ölçme yöntemi,
♦ Vickers sertlik ölçme yöntemi,
♦ Mikro- sertlik deneyi.
Sertlik ölçmeleri yapılırken kullanılan ölçme yöntemi ne olursa olsun, numunelerin üzerinde birkaç ölçme yapılıp ortalamasının alınması gerekir. Yapılan sertlik ölçümlerindeki değerler birbirinden çok farklı ise, farklı değer ortalamaya dahil edilmeyip bu farkın mevcudiyeti mutlaka belirtilmelidir.
1. BRİNELL SERTLİK ÖLÇME YÖNTEMİ:Bu ölçme, kalibrasyonu yapılmış bir cihaz kullanarak deneyi yapılacak malzemenin yüzeyine belirli bir yükün, belirli çaptaki sert malzemeden yapılmış bir bilya yardımıyla belirli süre uygulanmasından ve sonuç olarak meydana gelen iz’in çapının ölçülmesinden ibarettir. |
Standart deney şartlarında bilya çapı 10 mm, uygulanan yük 3000 kg, tatbik süresi 10-15 sn kadardır. Standard Brinell deneyinde kullanılan yükler 500, 1500 veya 3000 kg. dır. Yük, malzemeye yavaş yavaş artacak şekilde Uygulanmalı, darbeli yüklemeler önlenmelidir. Ayrıca yükün numuneye dik gelecek şekilde uygulanmasına dikkat edilmelidir. Yükün uygulama süresi, yumuşak metalle r dışında genellikle 10 -15 saniyedir. Yumuşak metaller için bu süre 30 saniye ve daha fazla olabilir. Meydana gelen izin çapı 2,5 – 0,0 mm (Bilya çapının % 25’i ile % 60’ı) arasında olacak şekilde deney yükü seçilir. İz çapında böyle bir alt sınırın belirtilmesi gereklidir, çünkü iz çapı küçüldükçe, deneydeki hata nisbeti artar, iz çapının üst sınırı da, bazı deney cihazlarında ucun hareket miktarı ile sınırlanmıştır.
Meydana gelen izin birbirine dik iki yönde çapı taksimatlı büyüteç ile ölçülür ve Brinell sertlik değerini tayin ederken bu iki ölçmenin ortalaması kullanılır. İz çapı en az 0,02 mm’lik bir doğrulukta ölçülür.
Belirli malzemenin farklı sertliklerini mukayese edebilmek için o malzemeye ait sertlik değerlerinin (Tablo 1)’de tavsiye edilen sınırlar içerisinde olabilecek şekilde, tek bir yük kullanarak ölçülmesi tavsiye edilir. [1]
Tablo 1 – standart Brinell Deneyinde Uygulanan Yüke Göre Tavsiye Edilen Sınır Değerler
Bilya çapı (mm) | Yük (Kg) | Tavsiye Edilen Sınır Brinell Sertlik Değeri |
10 | 3000 | 96 ile 600 |
10 | 1500 | 48 ile 300 |
10 | 500 | 16 ile 100 |
2. ROCKWELL SERTLİK ÖLÇME YÖNTEMİ
Rockwell sertlik değeri, malzeme üzerine, batıcı bir uç yardımıyla önce sabit belirli küçük bir yükle bastırıldığında meydana gelen izin dip kısmı başlangıç noktası alınarak, yük daha yüksek belirli bir derecere arttırılıp daha sonra tekrar önceki yüke dönülmek suretiyle, başlangıçtakiize nazaran meydana gelen iz derinliğindeki net artışla ters orantılı bir sayıdır.
Rockwell deneyi için kullanılan batıcı uçlar belirli çaplarda çelik bilyalarla, özel konik bir elmas uçtan ibarettir. Rockwell sertlik değerleri daima bir sembol harfle birlikte belirtilir ki bu sembol harf batıcı ucun tipini, kullanılan yükün miktarını ve kadran üzerinde okunacak bölümü belli eder.
Bilye tipi batıcı uçlar, 1.588 mm (1/16 inç), 3.175 mm u/8 inç,), 6.350 mm (1/4 inç) ve 12.700 mm (1/2 inç) çapında çelik bilyelerdir. Elmas batıcı uç ise 120 + 0.5° lik bir açı teşkil eden bir koni ile, tepe noktası 0.2 mm yarı çapında bir küre parçasından ibarettir.
Bilyelerin çapı normal değerden +0.0035 mm den fazla farklı olmamalıdır. Batıcı uç üzerinde toz, kir, gres ve tufal gibi yabancı maddeler bulunmamalıdır; bulunduğu takdirde sonuçlara etki eder.
Rockwell sertlik deneyi için (Şekil 2) önce 10 kg.’lık ki yük uygulanarak ilk yükleme yapılır. Bu suretle uç, malzeme üzerine oturur ve onu yerinde tutar. Siyah rakamlı bölüm üzerinde kadran sıfıra getirilir ve daha sonra büyük yük uygulanır. Bu büyük yük uygulanan toplam yük olup, derinlik ölçmesi sadece küçük yükten büyük yüke kadar artıştan ileri gelen derinlik artışına bağlıdır. Büyük yük uygulandıktan ve kaldırıldıktan sonra, standart işleme göre küçük yük hala uygulanır durumda iken, kadranın gösterdiği değer okunur.
Batıcı uç olarak çelik bilye kullanıldığı zaman büyük yük 100 kg olarak alınır, fakat gerektiği zaman diğer yükler de kullanılır. Ucu küresel konik elmas uç kullanıldığı zaman büyük yük, genel olarak 150 kg.
Batıcı uç sertliği ölçülecek yüzeye dik gelecek şekilde temas etmelidir.
Numune kalınlığı ne olursa olsun, sertlik bir tek kalınlık üzerinde ölçülmelidir. Kalınlık arttırma amacıyla üst üste konmuş malzemeler üzerinde ölçülen sertlik değerleri güvenli sayılmazlar.
Rockwell sertliğinin tayini sırasında meydana getirilen iz, kenara çok yakın olmayacağı gibi iki iz’de birbirine çok yakın bulunmamalıdır. [1]
3. VİCKERS SERTLİK ÖLÇME YÖNTEMİ
Vickers sertlik ölçme yöntemi, sertliği ölçülecek malzeme parçasının yüzeyine, tabanı kare olan piramit şeklindeki bir ucun belirli bir yük altında daldırılması ve yük kaldırıldıktan sonra meydana gelen izin köşegenlerinin ölçülmesinden ibarettir.
Vickers sertlik değeri, piramit şeklindeki dalıcı ucun belirli bir yük altında ve belirli bir süre uygulanması ile malzeme yüzeyinde meydana getirdiği izin büyüklüğü ile ilgili bir değerdir.
Meydana gelen iz. taban köşegeni (d) olan kare bir piramittir ve tepe açısı dalıcı ucun tepe açısının aynıdır = (136°). Vickers sertlik değeri, kg olarak ifade edilen deney yükünün (mm²) olarak ifade edilen iz alanına bölümüdür.
Vickers sertlik değeri işareti ile beraber bazen uygulanan yük ve yükün uygulama zamanını belirten sayısal işaretlerde ilave edilir. Örneğin; VSD /30 /20, /30 kg.’lık yükün 20 saniye süre ile uygulanması sonucu elde edilen Vickers sertlik değerini gösterir.
Deneyden sonra Vickers sertlik değerini bulmak için kare şeklindeki izin köşegenlerinihassas, bir şekilde ölçmek gerekir. Bu ölçme, alete ilâve edilmiş metalürji mikroskobu sayesinde yapılmaktadır; numune üzerinde meydana getirilen izin görüntüsü mikroskop yardımıyla ölçme ekranınaaktarılır. Ölçme ekranındaki hareketli iki cetvel yardımıyla köşegenlerin uzunlukları hassas bir şekilde ayrı ayrı ölçülüp ortalaması alınır. [1]
Vickers sertliği ölçüsü, geniş çubuklardan saçlara kadar her ölçüde malzeme çeşidine uygulanabilir. Genel olarak numunelerin alt ve üst yüzeyleri, yük bindiği zaman numune hareket etmeyecek veya kaymayacak şekilde düz olmalıdır. Kalınlık olarak da, piramit dalıcı ucun, numunenin öbür yüzeyinde bir çıkıntı meydana getirmeyecek derecede kalın olması yeterlidir.
4. MİKRO – SERTLİK DENEYİ
Bu deney, özellikle çok küçük numunelerin ve ince saçların sertliklerini ölçmede elverişlidir. Karbür ize, dekarbürize ve azotla sertleştirilmiş yüzeylerle, elektrolitik olarak kaplanmış malzemelerin sertlilikleri de bu deney ile tespit edilebilir. Ayrıca, metalik alaşımlarda fazların sertliklerinin tespitinde, segregasyonların ve cam, porselen, metalik karbürler gibi çok sert ve kırılgan malzemelerin sertliklerini ölçmede de kullanılır. Deney malzemesinin sertliğine göre seçilen uygun yükler için, batıcı ucun malzemeye girdiği derinlik hiç bir zaman “l” mikronu geçmez.
Mikro – sertlik aleti hassas bir alet olup kontrolü otomatiktir. Diğer sertlik ölçme aletlerinden farklı olan yanı, aletin komple metal mikroskobunu ihtiva etmesidir.
Sertliği ölçülecek numune mikroskobun tablasına oturtulur ve okülerde net görüntü elde edinceye kadar mikroskop tablas ı hareket ettirilir. Bundan sonra mikroskop tablası elle, sertlik ölçen kısmın altına getirilir ve düğmeye basarak sertlik ölçen ucun hareketi sağlanır. Uç, otomatik olarak numuneye batar ve 20 saniye sonra yine otomatik olarak geriye döner. Böylece numunenin üzerinde bir iz elde edilir. izin boyutlarını ölçmek için mikroskobun tablası yine elle objektifin altına getirilir ve okülerden iz gözlenir. Oküler üzerindeki özel taksimat ile izin boyutları tespit edilir.
Mikro – sertlik deneyi için iki standart uç kullanılır. Birincisi 136º’lik tabanı kare olan piramit uç (vickers ucu)dur.
Diğeri ise knoop ucu diye bilinen 172º 30’lik piramit ucudur. [1]
136º’lik uç malzeme üzerine kare şeklinde iz bırakmasına rağmen, knoop ucu eşkenar dörtgen şeklinde bir iz bırakır.
ÇEKME TESTİ NEDİR?
Çekme Deneyi Nedir?
Çekme Deneyi Nedir? | Gerilim testi olarak da bilinen Çekme Testi, kontrollü gerilimle bir numuneye kanıt amaçlı bir yük altında belli bir seviyeye kadar olarak veya tamamen malzeme kopana kadar malzemeye kuvvetin uygulandığı, numunenin davranışını belirlemek amacıyla yapılan yıkıcı bir mühendislik ve malzeme bilimi testidir.
Bu en yaygın mekanik test tekniklerinden biridir. Bir malzemenin ne kadar güçlü olduğunu ve kırılmadan önce ne kadar gerilebileceğini bulmak için kullanılır. Bu test yöntemi akma mukavemeti, nihai gerilme mukavemeti, süneklik, gerinim sertleştirme karakteristikleri, Young modülü ve Poisson oranını belirlemek için kullanılır.
Nihai Çekme Dayanımı
Bu, test sırasında bir numunenin maruz kaldığı maksimum strestir. Yani numunenin sahip olduğu maksimum çekme dayanımıdır. Bu, kırılgan, sünek veya her ikisinin özelliklerine sahip olmasına bağlı olarak kırılma sırasında numunenin mukavemetinden farklı olabilir. Bu malzeme özellikleri çevreye bağlı olarak değişebilir, örneğin aşırı sıcak veya soğuk koşullarda duruma bağlı olarak değişim gösterebilir.
Bu test metaller, plastikler, elastomerler, kağıt, kompozitler, kauçuklar, kumaşlar, yapıştırıcılar, filmler, vb. dahil olmak üzere çeşitli malzemeler üzerinde gerçekleştirilir.
Akma Dayanımı
Akma dayanımı, stres altında plastik deformasyonun meydana geldiği noktadır. Bu, ekstensometreler olarak bilinen cihazların kullanımı yoluyla ölçülen bir gösterge uzunluğu üzerinde test sırasında belirlenir.
Çekme Testi Nasıl Yapılır ?
Çekme deneyi için önce test edilecek malzemeden standartlara uygun bir çekme numunesi hazırlanır .
Çekme deney makinesinin çeneleri arasına düzgün ve ortalayacak bir
şekilde sıkıştırılan bu numune gittikçe artan bir yükle kopuncaya kadar çekilir.
Bu esnada uygulanan F yükü ile buna karşı malzemenin gösterdiği uzamalar (ΔL) cihaz ile ölçülür.
Deney sonucu elde edilen yük ( F ) ve uzama (ΔL) değerlerinden yararlanarak (F – ΔL) diyagramı elde edilir.
Bu diyagrama çekme diyagramı da denir.
Çekme Testi Sonuçları Neler İçerir?
Çekme testi yapıldıktan sonra, testin yapıldığı numuneye ait aşağıdaki sonuçlara ulaşılabilir.
Çekme testi şu sonuçları içerir:
• Maksimum Yük
• Maksimum Yük Sapması
• Maksimum Yükte Çalışmak
• Maksimum Uzama
• Kırılma Yükü
• Kırılma Sapması
• Elastik Modülü
Çekme Testi Neden Yapılır?
Çekme testi, bir malzemenin davranışını belirlemek ve mekanik özelliklerinin ayrıntılarını belirlememizi sağlar. Bu özellikler, malzemenin başarısız olduğu noktalar gibi detayların yanı sıra esneklik, gerilme ve akma mukavemeti modülü gibi özellikleri de verir. Ek olarak aldığımız bu değelerle bu detayları gösterecek bir grafik üzerinde bir gerilim / deformasyon eğrisi ile verilen bu noktaları grafik üzeriden çok daha rahat görebiliriz.
Çekme testinin aşağıdakileri içeren çeşitli kullanımları vardır:
• Bir uygulama için malzeme seçimi
• Bir malzemenin farklı kuvvetler altında nasıl performans göstereceğini tahmin etme
• Bir şartname veya sözleşme için standart gereksinimlerinin karşılanıp karşılanmadığını belirleme
• Yeni bir ürün için konsept kanıtı gösterme
• Önerilen bir patent için kanıtlama
• Bilimsel ve mühendislik işlevleri için standart kalite güvence verileri sağlama
• Farklı malzeme seçenekleri için teknik verilerin karşılaştırılması
• Yasal işlemlerde kullanım için kanıt sağlama
Çekme Testini Kullanmanın Avantajları Nelerdir?
Ekipmandaki kusurlar, bir ürünün üreticisi ve kullanıcısı için maliyetli ve tehlikeli olabilir. Çekme testi, bir malzemenin veya parçanın mühendislik gerilmesi ve diğer özelliklerini belirleyerek bu tehlikeyi büyük ölçüde azaltabilir. Yani malzemenin nasıl bir kalitede nasıl bir dayanıma sahip olduğunu öğrenmek istiyorsanız bu testi yapmanız sizin yararınıza olacaktır.
Çekme testi ayrıca tasarımcılara ve üreticilere yeni malzemeler ve özellikleri hakkında bilgi verir, böylece ileride kullanılmak üzere kaliteleri kendileri belirleyebilirler.
DIN EN ISO 6892-1, ASTM E 8 – Metali Oda Sıcaklığında Çekme Testi
Test Yönteminin Açıklaması
Çekme testi, bileşenlerin, günlük nesnelerin, makinelerin, araçların ve yapıların tasarımı ve yapımı için belirleyici öneme sahip olan metallerin uygulamaları için mukavemet ve uzama parametrelerini belirleyen, dünya çapında en önemli ve en sık kullanılan mekanik-teknolojik testtir.
Test görevi, malzeme parametrelerini güvenilir ve tekrarlanabilir bir şekilde belirlemek ve uluslararası karşılaştırılabilirliği sağlamaktır.
Tek eksenli çekme testi, akma noktası veya dayanım gerilmesi, gerilme mukavemeti ve kopmada uzama için karakteristik değerleri belirleme yöntemidir.
Ek olarak, daha düşük akma noktası, akma noktası uzaması ve maksimum kuvvette uzama belirlenir.
Çekme testi metal ISO 6892 ve ASTM E 8 – sıcaklık aralığına göre farklılaşma
Metal üzerindeki çekme testleri için, standardizasyon, çekme testlerinin gerçekleştirildiği dört sıcaklık aralığını birbirinden ayırır: oda sıcaklığı, yüksek sıcaklık, düşük sıcaklık ve sıvı helyum sıcaklığı. Sıvı helyumun farklı sıcaklık aralıkları ve ortamı, test sistemlerine ve hazırlanacak numuneleri içeren test yöntemine çok farklı talepler getirir. Bu nedenle uluslararası ISO standardı, her biri yukarıda belirtilen sıcaklık aralıklarını ele alan dört farklı bölüme ayrılmıştır.
ISO 6892-1 Oda sıcaklığında test yöntemi
ISO 6892-2 Yüksek sıcaklıkta test yöntemi
ISO 6892-3 Düşük sıcaklıklarda test yöntemi
ISO 6892-4 Sıvı helyumda test yöntemi
Bu uluslararası geçerliliğe sahip ISO standartlarına ek olarak, Amerikan ASTM, Avrupa EN, Japon JIS ve
Çin GB/T gibi ulusal standartlar da uluslararası olarak kullanılmaktadır. Özel uygulama alanları için,
örn.havacılıkta, başka spesifik standartlar önemli veya gerekli olabilir.
DIN EN ISO 6892-1, ASTM E 8 Çekme Testi
Metal veya metal malzemeler üzerindeki çekme testleri temel olarak normlar DIN EN ISO 6892-1 ve ASTM E 8’e dayanmaktadır.Her iki standart da numune şekillerini ve testlerini belirtir.Standartların amacı, test prosedürünü, farklı test sistemleri kullanıldığında dahil belirlenecek karakteristik değerlerin karşılaştırılabilir ve doğru kalacağı şekilde tanımlamak ve tanımlamaktır.Bu aynı zamanda, normatif gerekliliklerin önemli etkileyen faktörleri ele aldığı ve genel olarak gereklilikleri formüle ettiği, böylece teknik gerçekleştirmeler ve yenilikler için yeterli kapsam olduğu anlamına gelir.
Metal çekme testinden önemli parametreler şunlardır:
Akma noktası; daha doğrusu üst ve alt akma noktası (ReH ve ReL)
Uzama noktası; genellikle %0,2 plastik uzamada “Yedek akma noktası” olarak belirlenir (Rp0.2)
Akma noktası uzaması; daha doğrusu akma noktası ekstansometre uzaması, çünkü sadece bir ekstansometre (Ae) yardımıyla belirlenebilir
Çekme dayanımı (Rm)
Tek tip genişleme (Ag)
Kopma noktasındaki uzama (A), bu sayede ölçüm uzunluğu ile ilgili normatif sabitlemeler belirleyici öneme sahiptir.
Farklı malzeme konsolidasyonu ile çekme dayanımı
Belirgin bir akma noktasına sahip metalik malzemeler için çekme mukavemeti (maksimum çekme kuvveti), üst akma noktasından sonra elde edilen en yüksek kuvvet olarak tanımlanır.
Akma noktasının aşılmasından sonraki en yüksek çekme kuvveti, hafif sertleşen malzemeler durumunda da akma noktasının altında olabilir, yani bu durumda çekme mukavemeti, üst akma noktası değerinden daha düşüktür.
Resimde, gerilme-uzama diyagramı, akma noktasından sonra yüksek sertleşmeye (1) ve çok düşük sertleşmeye (2) sahip bir eğri göstermektedir.
Akma noktası ve ardından voltaj düşüşü olan metal için gerilme mukavemeti akma noktasındaki gerilime karşılık gelir.
Akma dayanımı (ReH ve ReL), uzama dayanımı (Rp ve Rt) ve çekme dayanımı (Rm)
Akma noktası ve gerilme mukavemetinin belirlenmesi için yalnızca kesin bir kuvvet ölçümü gereklidir, diğer tüm parametreler için test sırasında bir ekstansometre ile bir (otomatik) gerinim ölçümü veya numune / numune kalıntısını aldıktan sonra manuel bir gerinim ölçümü gerekir.
Akma noktası neyi tanımlar?
Akma dayanımı Re (akma dayanımı) bir malzeme parametresidir ve çekme testinin (örn. Standart seri ISO 6892 (metalik malzemeler için) veya standart seri ISO 527 (plastikler ve kompozitler için)) yardımıyla belirlenir. Akma dayanımı MPa (Megapaskal) veya N/mm² cinsinden verilir.
Bir üst akma noktası ReH ve daha alt bir akma noktası ReL sıklıkla belirlenebilir.
Üst akma noktası, çekme gerilimi altındaki bir malzemede kalıcı plastik deformasyonun oluşmadığı gerilimi gösterir. Malzeme deforme olur, ancak çekme gerilimini bıraktıktan sonra orijinal şekline geri döner. Üst akma noktası aşıldığında plastik, yani kalıcı şekil değişikliği başlar; gerilme testinde numune geri çevrilemez şekilde uzatılır.
Akma dayanımı oranı, akma dayanımı Re vegerilme dayanımı Rm’den hesaplanabilir: Re / Rm
Akma dayanımı oranı , gerilme dayanımına kadar sertleşmenin bir ölçüsüdür. Akma mukavemeti oranı, malzemenin arızalanması açıkça ortaya çıkıncaya kadar bir yapı için ne kadar gerilme gerilmesinin mevcut olduğunu gösterir.
Genellikle malzemelerdeki akma noktası belirgin değildir ve bu nedenle çekme testlerinde net bir şekilde belirlenemez. Bu durumlarda, daha sonra eşdeğer akma mukavemetleri veya akma mukavemetleri belirlenir. Kural olarak, akma mukavemeti %0,2 plastik uzamada belirlenir, dolayısıyla parametre Rp 0,2 ile gösterilir.
Üst akma noktası ReH
Net ilk düşüşünden önceki en yüksek gerilim, üst akma noktası ReH olarak adlandırılır. Bu noktadan itibaren malzeme plastik olarak deforme olur. Akma noktası çok belirgin ise, malzeme akmaya başlar ve gerilim biraz azalır, ancak uzama daha da artar. Akış sırasındaki en düşük çekme gerilmesi, düşük akma noktası ReL’ye karşılık gelir. Bu etki yalnızca alaşımsız veya düşük alaşımlı çeliklerde görülür.
Üst akma noktası, akıştan önceki en yüksek çekme gerilmesidir ve metal çekme standardı ISO 6892-1 tarafından aşağıdaki gibi tanımlanır: Maksimum gerilime ulaştıktan sonra, gerilme tekrar üst akma noktasını aşmadan en az % 0,5’lik bir gerilim düşüşü ve ardından en az % 0,05’lik bir akış olmalıdır.
Üst germe sınırın hesaplanması
Üst akma noktası ReH, çekme testinin gerilme-gerinim diyagramından belirlenir:
Üst akma noktası ReH = üst akma noktasındaki maksimum kuvvet FeH / numune ilk kesiti S0
Düşük akma noktası ReL
Düşük akma noktası ReL, üst akma noktası ReH’den sonra malzeme akış alanındaki en küçük gerilimdir, bu nedenle geçici etkiler (örneğin, yürürlükteki değişiklik nedeniyle) hesaba katılmamalıdır.
Üst akma noktasının tespit edilmemesi (kuvvet düşüşünün %0.5’ten az olması) veya akışın daha geniş bir alan üzerinde yaklaşık olarak sabit bir kuvvetle meydana gelmesi durumunda, bu gerilim değeri genellikle sadece akma noktası Re olarak anılır.
Alt germe sınırın hesaplanması
Alt akma noktası ReL, çekme testinin gerilme-gerinim diyagramından belirlenir:
Alt akma noktası ReL = üst akma noktasındaki maksimum kuvvet FeL / numune ilk kesiti S0
Minimum akma dayanımı nedir?
Minimum akma dayanımı , bir yandan, uygun ısıl işlemle belirli bir malzeme için kararlı bir şekilde ulaşılan veya aşılan minimum akma dayanımının değeri ve diğer yandan bileşenlerin ve destekleyici yapıların inşası için temel olarak kullanılması gereken bir maksimum gerilme değeridir, böylece kalıcı deformasyon bileşenlerin ve yapıların amaçlanan kullanımı güvenli bir şekilde önlenebilir.
Minimum akma dayanımı, malzeme tedarikçisi için ulaşılması gereken minimum değer ve tasarımda aşılmaması gereken malzeme kullanıcısı için maksimum değer olur.
Çelikte akma noktası ne anlama geliyor?
Akma noktası, malzemenin elastik davranışının sonu ve plastik davranışın başlangıcı anlamına gelir. Bu, akma noktası aşıldığında, malzemenin geri döndürülemez bir şekilde, yani kalıcı olarak plastik olarak deforme olduğu anlamına gelir.
Kural olarak, akma noktası yerel veya kısmen aşıldığında bile bileşenler ve yapılar artık güvenli bir şekilde kullanılamaz.
Akma dayanımı Rp0.2 nedir?
Akma mukavemeti Rp0,2, plastik ekstansometre geriliminin % 0,2’lik ekstansometre ölçüm uzunluğunun bir yüzdesine karşılık geldiği tek eksenli çekme testindeki çekme gerilimidir.
Soğuk haddelenmiş veya soğuk şekillendirilmiş malzemelerin belirgin bir akma noktası yoktur. Bu malzemeler için genellikle % 0,2 kalıcı gerilme (Rp0,2) belirlenir ve belirtilir. Bu % 0,2 verim noktası, her zaman gerilim-gerinim diyagramından açıkça belirlenebilir (bu, her zaman bir üst akma noktasında geçerli değildir).
% 0,2 prova gerilimi, numunenin plastiğe maruz kaldığı gerilmedir, yani % 0,2’lik geri döndürülemez gerinim (numunenin başlangıç uzunluğuna bağlı olarak).
TUZ KOROZYON NEDİR?
Tuz Korozyon Testi
Çok çeşitli malzemelerin ve yüzey kaplamalarının beklenen korozyon direncine ilişkin çok sayıda test verisi ile uzun bir geçmişe sahiptir. Bu tür tuz püskürtme testleri genellikle aşağıdaki test koşullarının oluşturulmasını gerektirir:
- Ağırlıkça %5’lik bir tuzlu su çözeltisi, sıkıştırılmış hava ile test edilecek numuneleri içeren kapalı bir test odasına yönlendirilen bir sprey (“sis” veya “sis” olarak da bilinir) halinde atomize edilir. atomize tuz spreyinin altında ve bu nedenle doğrudan onun tarafından etkilenmez.
- Bu şekilde oluşturulan tuz spreyi, test edilen numunelerin üzerine 1.0 ila 2.0ml/80cm2/saat oranında ‘düşürür’. Genel olarak ve aksi belirtilmedikçe, bu düşüşün pH’ı nötr olmalı ve pH 6,5 ila 7,2 arasında kontrol edilmelidir.
- Tuz püskürtme atomizasyonu, test süresince süreklidir. Test süresi, test numunesinin tipine ve amaçlanan uygulamaya göre değişir ancak genellikle 24 saatin katları halinde verilir.
Genel olarak ve aksi belirtilmedikçe, test odası sıcaklığı +35C’de kontrol edilecek ve nem, %95-100 RH’de muhafaza edilecektir. Bu koşullar, test süresince sürekli olarak korunur.
Test çözeltisini oluşturmak için kullanılacak tuzun ve suyun saflığı gibi diğer parametreler de kontrol edilir ve
hazne içindeki test numunelerinin konumu/yönü. Amaç, sadece test edilen numunelerin korozyon direncinin değişebileceği ölçüde tüm test değişkenlerini kontrol etmektir.
Tuz püskürtme testi için belirtilen test koşulları, doğal olarak oluşan bir ortam için tipik olmadığından, bu tür test, test edilen numuneler için ‘gerçek dünya’ hizmet ömrü beklentisini tahmin etmenin güvenilir bir yolu olarak kullanılamaz. Ancak, elde edilen gerçek sonuçların beklenen sonuçlarla (belki de önceki testlerden) karşılaştırıldığı karşılaştırmalı testler yapmak için kullanışlıdır. Bu nedenle ana uygulaması kalite denetimi rolündedir. Bu nedenle, örneğin, bir üretim sürecini ‘polis’lemek ve korozyon direncini etkileyebilecek olası üretim sorunları veya kusurları konusunda önceden uyarmak için bir püskürtme testi kullanılabilir.
‘Gerçek dünya’ aşındırıcı koşullarla korelasyonu olmamasına rağmen, tuz püskürtme testi, çeşitli yüzey kaplamaları ve/veya prosesler için nispi korozyon direncini denetlemenin etkili bir kalite aracı olarak çok çeşitli endüstrilerde popülerliğini korumaktadır. ki bunlar uygulanır.
Modifiye Tuz Korozyon Testleri
ASTM G85, modifiye tuz püskürtme testlerini kapsayan en popüler küresel test standardıdır. ASTM G85’te A1’den A5’e kadar olan ekler olarak anılan bu tür toplam beş test vardır. Bu modifiye edilmiş testlerin çoğu, doğal olarak meydana gelen korozyonun etkilerini taklit edebilen ve bu etkileri hızlandırabilen bir korozyon testine olan ihtiyacı ele almak için orijinal olarak belirli endüstri sektöründe ortaya çıkmıştır.
ASTM G85 Ek A1 – Asetik asit tuzu püskürtme testi
Bu test, yüksek sıcaklıkta asetik asit tuzu sprey iklimine maruz kaldığında çelik ve çinko bazlı döküm üzerine dekoratif krom kaplamanın korozyona karşı göreceli direncini belirlemek için kullanılabilir. Bu test aynı zamanda bir ASS testi olarak da adlandırılır.
Tuz sprey testi, kaplanmış numunelerin korozyon direncini kontrol etmek için kullanılan standart bir test yöntemidir. Kaplamalar, çelik, zamak veya pirinçten yapılmış metal parçalara korozyon direnci sağlar. Kaplamalar kullanımdaki parçanın ömrü boyunca yüksek korozyon direnci sağlayabileceğinden korozyon direncini diğer yollarla kontrol etmek gerekir. Tuz püskürtme testi, koruyucu bir kaplama olarak kullanımındaki uygunluğunu tahmin etmek için kaplanmış numunelere aşındırıcı bir saldırı üreten hızlandırılmış bir korozyon testidir. Korozyon ürünlerinin (oksitlerin) görünümü belli bir süre sonra değerlendirilir. Test süresi kaplamanın korozyon direncine bağlıdır; kaplamaya karşı daha fazla korozyon direnci, korozyon belirtileri göstermeden test süresinin uzamasına neden olur.
Tuz sprey testi popüler, çünkü ucuz, hızlı, iyi standardize edilmiş ve makul bir şekilde tekrarlanabilir. Bununla birlikte, korozyon çok karmaşık bir prosestir ve etkilenebildiğinden, tuz püskürtme testindeki süre ile bir kaplamanın beklenen ömrü arasında (özellikle kurutma devirleri dayanıklılık açısından önemli olan sıcak daldırma galvanizli çeliklerde) zayıf bir korelasyon vardır Birçok dış faktörle. Bununla birlikte, bitmiş yüzeylerin veya parçaların korozyon direncinin değerlendirilmesi için endüstriyel sektörde tuz püskürtme testi yaygın olarak kullanılmaktadır.
Test etme aparatı, tuzlu bir çözeltinin (çoğunlukla,% 5 sodyum klorürün bir çözeltisi) bir meme vasıtasıyla atomize edildiği kapalı bir deney odasından oluşur. Bu, haznede yoğun salyangoz sisleyici bir korozif ortam oluşturur, böylece içinde maruz kalan parçalar ciddi aşındırıcı koşullara maruz kalır.
Deney numuneleri, 35 ± 2 0C sıcaklıktaki kabinde % 5 konsantrasyondaki tuzlu su istenen deney süresi boyunca kesintisiz olarak kaplamalı parça üzerine püskürtülür. Deney sonunda kaplamalı parçalar, ISO 4628-2 Kabarcıklanma Derecesi, ISO 4628-3 Paslanma Derecesi, ISO 4628-4 Çatlama Derecesi, ISO 4628-5 Pullanma Derecesi, ISO 4828-8 Bir Çizik Etrafında Tabakalara Ayrılma ve Korozyon Derecesinin Değerlendirilmesi ve ISO 4628-10 Filiform Korozyon standartlarınca yada ASTM standartları gereğince incelenip yorumlanır.
Korozyon standartları EN ISO 9227 yanı sıra bir çok standart da vardır. Bunların bazıları aşağıdaki gibidir.
- Çevrimsel Korozyon Testi (DIN 50018)
- Tuz Püskürtme Testi (ASTM B117, ISO 9227)
- Nem Testi (ASTM D2247, ISO 6270-2)
- VDA 233-102
- ISO 11997-2
- EN ISO 3231
- ISO 2812-2:
- VDA 621-412:
- CETP 00.00-L-467 Laboratuvar Ortamında Hızlandırılmış Çevrimsel Korozyon Testi
- ASTM D610 Boyalı Çelik Yüzeylerde Aşınma Derecesini Değerlendirme
- ISO 16750-5 Elektrikli ve Elektronik Cihazlar İçin Çevresel Koşullar ve Testler
- DIN ISO 11664-4 Kolorimetrik Analiz ve Renk Ölçümü
- DIN 67530 Boya Kaplamaları ve Plastiklerin Plane Yüzeylerinin Değerlendirilmesi
- ISO 7591 Motorlu Taşıtlar ve Römorkları İçin Retro-Reflektif İşaretlemelerin Kullanımı
- DIN 75220 Güneş Işığı Simülasyonu İle Araç Komponentlerini Yaşlandırma
- MIL-STD-810F Method 505.4 Solar Radiation
- EN 60529
- ISO 20653 Toz ve Suya Karşı Derecelendirme Testi